High Power Bipolar Stepper Motor Driver with SPI Interface
- Rajkumar Sharma
- 201 Views
- medium
- Tested
- SKU: EL138922
- Quote Now
This is a compact high-power stepper motor driver built for bipolar stepper motors. The driver can be controlled using a serial communication interface (SPI). It combines a flexible ramp generator for automatic target positioning with the industry’s most advanced stepper motor driver. Using external transistors, the driver ensures absolutely noiseless operation combined with maximum efficiency and the best motor torque. High integration, high energy efficiency, and a small form factor enable miniaturized. The complete solution reduces the learning curve to a minimum while giving the best performance in class. The project has the option to interface an external incremental encoder for easy control of position and step-loss operations.
Features
- Power Supply Motor 9 to 36V DC
- 2.8A Continues Current (3.1A Peak)
- Configuration & Control via SPI
- S/D mode selectable via solder option
- Header Connectors for All signal Inputs
- Screw Terminal Connectors for Power Supply and Easy Motor Connections
- Low Ohmic MOSFETS for High Efficiency and Low Heat
- On Board Power LED
- Encoder Interface and 2xRef-Switch Input
- Highest Resolution 256 Microsteps Per Full Step
- Step/Dir Interface with microstep interpolation MicroPlyer™
- Motion Controller with SixPoint™ramp
- StealthChop2™ for quiet operation and smooth motion
- Resonance Dampening for mid-range resonances
- SpreadCycle™ highly dynamic motor control chopper
- DcStep™ load-dependent speed control
- StallGuard2™ high precision Sensorless motor load detection
- CoolStep™ current control for energy savings up to 75%
- Passive Braking and freewheeling mode
- Full Protection & Diagnostics
- PCB Dimensions 57.79 x 43.18mm
- 4 x 3MM Mounting Holes
Connections and Other Details
- P1: Pin 1 = DIAG, Pin 2 = GND
- P2: Pin 1 = GND, Pin 2 = VCC 3.3V/5V DC Input
- P3: Pin 1 = REFR, Pin 2 = REFL, Pin 3 = DRV_ENB, Pin 4 = CLK16, Pin 5 GND
- P4: Pin 1 = CSN, Pin 2 = SCK, Pin 3 = SDI, Pin 4 = SDO
- P5: Pin 1 = Encoder A, Pin 2 = Encoder B, Pin 3 = Encoder N
- P6: Pin 1 = GND, Pin 2 = Motor Supply + 9V to 36V DC
- P9: Pin 1 = Motor B2, Pin 2 = Motor B1, Pin 3 = Motor A2, Pin 4 = Motor A1
- D1: VCC Power LED
Mode of Operation
MODE 1: Full Featured Motion Controller & Driver
All stepper motor logic is completely within the TMC5160. No software is required to control the motor – just provide target positions. Enable this mode by tying low pin SD_MODE. Install Resistor R2 0 Ohms to select this mode. Do not install R1.
MODE 2: Step & Direction Driver
An external high-performance S-ramp motion controller like the TMC4361 or a central CPU generates step & direction signals synchronized to other components like additional motors within the system. The TMC5160 takes care of intelligent current and mode control and delivers feedback on the state of the motor. The Micro Plyer automatically smoothens motion. Tie SD_MODE high. Install Resistor R1 0 Ohms to select this mode. Do not install R2.
Mode Selection
- Soldering R2 / not R1 = Internal ramp generator active with Trinamic’s 6-point-ramp (default mode)
- Soldering R1 / not R2 = Step/Direction interface active for use with external motion controller (STEP =REFL, DIR = REFR)
Automatic Standstill Power Down
An automatic current reduction drastically reduces application power dissipation and cooling requirements. Modify stand still current, delay time and decay via register settings. Automatic freewheeling and passive motor braking are provided as an option for stand still. Passive braking reduces motor standstill power consumption to zero, while still providing effective dampening and braking! An option for faster detection of standstill is provided for both, ramp generator and STEP/DIR operation.
Encoder Interface
TMC5160 board provides an encoder interface for external incremental encoders. The encoder allows automatic checking for step loss and can be used for homing of the motion controller (alternatively to reference switches), or for software-controlled correction of step-loss or position stabilization. Its programmable pre-scaler allows the adaptation of the encoder resolution to the motor resolution. A 32-bit encoder counter is provided.
Key Concepts
The TMC5160 board implements advanced features which are exclusive to TRINAMIC products. These features contribute toward greater precision, greater energy efficiency, higher reliability, smoother motion, and cooler operation in many stepper motor applications.
- StealthChop2™ No-noise, high-precision chopper algorithm for inaudible motion and inaudible standstill of the motor. Allows faster motor acceleration and deceleration than StealthChop™ and extends StealthChop to low stand still motor currents.
- SpreadCycle™ High-precision chopper algorithm for highly dynamic motion and absolutely clean current wave. Low noise, low resonance, and low vibration chopper.
- DcStep™ Load dependent speed control. The motor moves as fast as possible and never loses a step.
- StallGuard2™ Sensorless stall detection and mechanical load measurement. CoolStep™ Load-adaptive current control reducing energy consumption by as much as 75%.
- MicroPlyer™ Microstep interpolator for obtaining full 256 microstep smoothness with lower resolution step inputs starting from fullstep
In addition to these performance enhancements, TRINAMIC motor drivers offer safeguards to detect and protect against shorted outputs, output open circuit, overtemperature, and undervoltage conditions for enhancing safety and recovery from equipment malfunctions.
Control Interfaces
The TMC5160 board supports both, an SPI interface and a UART based single wire interface with CRC checking. Additionally, a standalone mode is provided for pure STEP/DIR operation without use of the serial interface. Selection of the actual interface is done via the configuration pins SPI_MODE and SD_MODE, which can be hardwired to GND or VCC_IO depending on the desired interface.
SPI Interface
The SPI interface is a bit-serial interface synchronous to a bus clock. For every bit sent from the bus master to the bus node another bit is sent simultaneously from the node to the master. Communication between an SPI master and the TMC5160 node always consists of sending one 40-bit command word and receiving one 40-bit status word.
The TMC5160 scores with complete motion controlling features, powerful external MOSFET driver stages, and high-quality current regulation. It offers a versatility that covers a wide spectrum of applications from battery powered high efficiency systems up to embedded applications with 10A or more motor current per coil. The TMC5160 contains the complete intelligence which is required to drive a motor. Receiving target positions, the TMC5160 manages motor movement. Based on TRINAMICs unique features StallGuard2, Cool Step, DC Step, Spread Cycle, and Stealth Chop, it optimizes drive performance. It trades off velocity vs. motor torque, optimizes energy efficiency, smoothness of the drive, and noiselessness. The small form factor of the TMC5160 keeps costs down and allows for miniaturized layouts. Extensive support at the chip, board, and software levels enables rapid design cycles and fast time-to-market with competitive products. High energy efficiency and reliability deliver cost savings in related systems such as power supplies and cooling.
Schematic
Parts List
NO. | QNTY. | REF. | DESC | MANUFACTURER | SUPPLIER | SUPPLIER PART NO |
---|---|---|---|---|---|---|
1 | 4 | C1,C5,C7,C8 | 100nF/50V CERAMIC SMD SIZE 0805 | YAGEO/MURATA | DIGIKEY | |
2 | 2 | C2,C3 | 2u2/50V CERAMIC SMD SIZE 0805 | YAGEO/MURATA | DIGIKEY | |
3 | 1 | C4 | 470nF/50V CERAMIC SMD SIZE 0805 | YAGEO/MURATA | DIGIKEY | |
4 | 1 | C6 | 22nF/50V CERAMIC SMD SIZE 0805 | YAGEO/MURATA | DIGIKEY | |
5 | 1 | C9 | 1uF/50V CERAMIC SMD SIZE 1206 | YAGEO/MURATA | DIGIKEY | |
6 | 1 | C10,C15,C16 | 10uF/50V CERAMIC SMD SIZE 1206 | YAGEO/MURATA | DIGIKEY | |
7 | 4 | C11,C12,C13,C14 | 220nF/50V CERAMIC SMD SIZE 0805 | YAGEO/MURATA | DIGIKEY | |
8 | 4 | R7,R8,R9,R10 | 47E 5% SMD SIZE 0805 | YAGEO/MURATA | DIGIKEY | |
9 | 1 | C17 | 470uF/50V ELECTROLYTIC THT | PANASONIC | DIGIKEY | P10400TB-ND |
10 | 1 | D1 | LED SMD RED SIZE 0805 | OSRAM | DIGIKEY | 475-1278-1-ND |
11 | 1 | IC1 | TMC5160A-TA | ANALOG DEVICE | DIGIKEY | 175-TMC5160A-TA-ND |
12 | 1 | P1 | 2 PIN MALE HEADER PITCH 2.54MM | WURTH | DIGIKEY | 732-5315-ND |
13 | 1 | P2 | 2 PIN MALE HEADER PITCH 2.54MM | WURTH | DIGIKEY | 732-5315-ND |
14 | 1 | P3 | 5 PIN MALE HEADER PITCH 2.54MM | WURTH | DIGIKEY | 732-5318-ND |
15 | 1 | P4 | 4 PIN MALE HEADER PITCH 2.54MM | WURTH | DIGIKEY | 732-5317-ND |
16 | 1 | P5 | 3 PIN MALE HEADER PITCH 2.54MM | WURTH | DIGIKEY | 732-5316-ND |
17 | 1 | P6 | 2 PIN SCREW TERMINAL PITCH 5.08MM | PHOENIX | DIGIKEY | 277-1247-ND |
18 | 2 | P9 | 2X2 PIN SCREW TERMINAL PITCH 5.08MM | PHOENIX | DIGIKEY | 277-1247-ND |
19 | 4 | Q1,Q2,Q3,Q4 | SI4288 OR AO4882 | VISHAY | DIGIKEY | SI4288DY-T1-GE3CT-ND |
20 | 2 | R1,R2 | 0R SMD SIZE 0805 | YAGEO/MURATA | DIGIKEY | |
21 | 8 | R3,R4,R5,R6,R13,R14,R15,R16 | 22E 5% SMD SIZE 0805 | YAGEO/MURATA | DIGIKEY | |
22 | 2 | R11,R12 | 75mR 1% 2W SMD SIZE 2512 | YAGEO/MURATA | DIGIKEY | |
23 | 1 | R17 | 2.2E 5% SMD SIZE 0805 | YAGEO/MURATA | DIGIKEY | |
24 | 1 | R18 | 1K 5% SMD SIZE 0805 | YAGEO/MURATA | DIGIKEY |
Connections
Multiple Stepper Motors
Block Diagram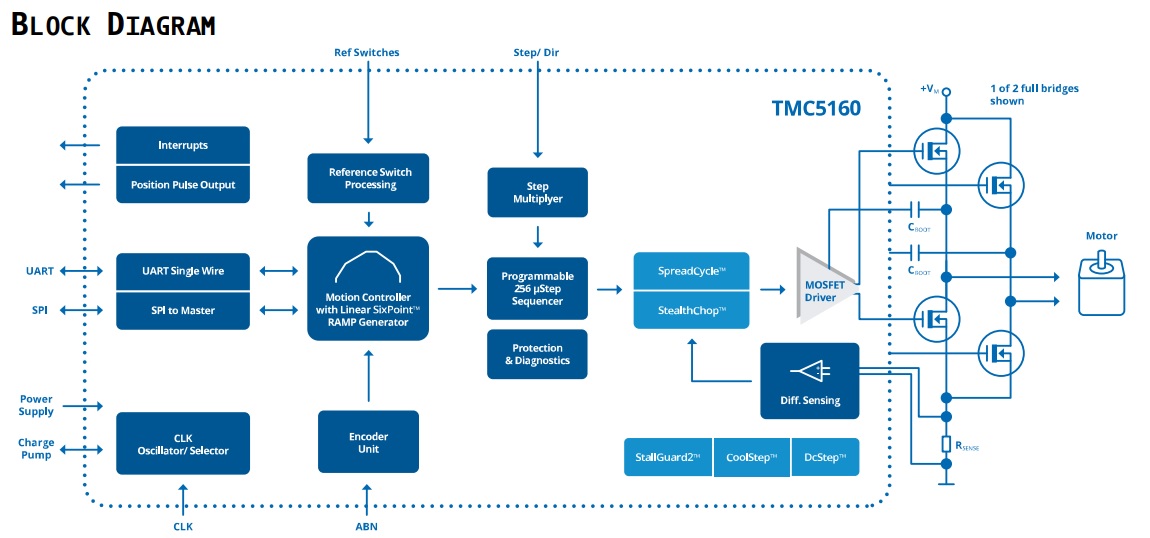
Gerber View
Photos
Video